Connector Grease Case Studies
Nye's ability to innovate, adapt, and develop solutions is as much in evidence today as it has been at any time during our history. Starting in the eighties, Nye connector greases were used in automobiles as field fixes for ignition module failures by sealing against any intrusion of water into the electronic modules. Nye dielectric greases continue to be used to resolve major automotive recalls to prevent short circuits that cause control module failures. As well, Nye dielectric greases ensure reliable performance in aviation, medical and semiconductor electronic applications.
Water Resistant Grease for Printed Circuit Boards
Background
One of Nye’s long-standing OEM customers manufactures vehicles using components from other suppliers. In one of their vehicles, they experienced short circuiting within their printed circuit boards, which lead to a recall of affected vehicles. When connectors within circuit boards are exposed to water, they can short circuit immediately and/or become corroded. Dealerships were unable to access the circuit board in recalled vehicles because a protective casing was built around the component. The Automotive OEM approached Nye to find a lubricant and dispensing option that could reach the hard to access area and solve the short circuit problem.
Challenges
- Can the lubricant protect the electrical contacts from water?
- Can Nye provide a dispensing solution that reaches these circuit boards?
Solution
NyoGel® 760G, 55cc Syringe
A silica thickened, medium viscosity, synthetic hydrocarbon grease.
- Excellent water resistance that protects contacts from short circuiting
- Syringe with metal tip allows dealerships to easily insert the lubricant into the circuit board
- Universal standard for dielectric grease specified by leading OEM’s
- Specifications: Ford: WSB-M1C239-A, GM: 9986087, & FCA: MS-9496
Results
Dealerships were able to successfully dispense NyoGel®760G into the printed circuit board of recalled vehicles because of the metal tip included in the design of the 55cc syringe. The supplier of these circuit boards was also able to use NyoGel®760G to lubricate components during manufacturing so that this problem would not arise in the future.
Protecting Transistors in Medical Devices Against Moisture
Background:
A medical device manufacturer approached Nye in search of a lubricant for their new transistor design. The transistors within this Saline Solution IV were located on a printed circuit board that was positioned next to a tube containing saline. The manufacturer was concerned that the coating on their PCB would not sufficiently prevent saline intrusion. Connector lubricants can act as a seal to keep dirt and moisture away from critical components. This customer needed a biocompatible lubricant that would seal the transistors and protect them from saline, water intrusion, and corrosion.
Challenge:
- Can the lubricant seal the transistor to keep out saline and prevent corrosion?
- Can we provide a small dispensing option for hand-held application?
Solution:
NyeMed® 7560, 10cc Syringe
A medium viscosity, UV-dyed, synthetic hydrocarbon grease
- Provides an environmental seal to protect against moisture and oxidation
- Biocompatible against three ISO 10993 standards
- Does not swell most plastics and elastomers
- UV dye enhances tracing and visualization
Results
Given the customer’s operating conditions, Nye provided a sample of NyeMed® 7560, a biocompatible lubricant with proven success in cable and connector applications. The customer conducted stringent validation testing which included immersing the lubricant in saline. NyeMed® 7560 passed these tests, proving that our lubricant prevented corrosion, did not interfere with electric signals, and was compatible with PCB materials. The customer implemented NyeMed® 7560 in their design and remains satisfied with its performance.
Preventing Fretting Corrosion in Electronic Control Modules
Background:
Electronic control modules (ECMs) perform various functions in automotive vehicles and protecting these components from failure has become even more important with the proliferation of electric vehicles. A leading OEM came to Nye after they noticed one of their vehicles ECMs sent an increased number of diagnostic codes related to open connections.
After further investigation they realized the connectors had experienced fretting corrosion, or minute vibrations that create oxide-build up that eventually leads to signal loss. The OEM was concerned that this would lead to braking-related safety issues including cruise control, lights, shifting out of park, etc. They approached Nye to see if we had a grease that would prevent fretting corrosion and restore connectivity to affected vehicles.
Challenge:
- Can Nye’s grease prevent fretting corrosion to eliminate oxide buildup around the connector terminals?
- Can we provide a grease that exhibits material compatibility with the plastics and elastomers used in the connector and control module housings?
Solution
NyoGel® 760G
A silica thickened, medium viscosity, synthetic hydrocarbon grease.
- Formulated to prevent fretting corrosion
- Compatible with most plastics and elastomers
- Copper passivator prevents copper corrosion
- Provides lifetime lubrication for lasting connections
Results
Nye recommended that the OEM use NyoGel® 760G, our industry standard grease for connector applications, and completed in-house validation tests for material compatibility, fretting protection, and copper corrosion protection. The OEM ultimately chose NyoGel® 760G as their connector solution because it provided the necessary fretting protection against vehicle vibration to eliminate oxide buildup around the terminals. NyoGel® 760G is now the OEMs go-to solution for recalls and to protect other control modules from failure.
Resolving Rack Equipment Power Failures
Background
A leader in integrated cloud technology noticed that the backup servers in their data centers were being used much too frequently because their primary servers were experiencing power failures. Upon inspection, they soon discovered that the busbar and crown clip connection for the primary server had corrosion build up. They attributed this problem to fretting corrosion, or micro-motions that wear contacts and expose fresh layers of metal to oxidation, eventually creating an open connection. The provider determined that the micromotion occurred during shipping and regular operation. After their manufacturing partner recommended our connector greases, an engineer contacted Nye to see if we could provide a solution that would protect future power connections from fretting corrosion and restore reliable connectivity to damaged connectors in the field.
Challenge
- Can our industry proven lubricant protect electrical contacts from fretting corrosion and prevent further power failures in the field?
Solution
NyoGel® 760G
A silica thickened, medium viscosity, synthetic hydrocarbon grease for lubricating contacts.
- Extends the reliability of connectors
- Prevents fretting wear
- Insulates from short circuits
- Protects from environmental exposure
Results
To validate our solution, our Application and Test Design Engineers used our fretting corrosion test rig and modified the design using custom fixtures to replicate the customer's application conditions. Our team ran two tests, one on unlubricated contacts and one with contacts lubricated with NyoGel® 760G. NyoGel® 760G was run for 5.8M cycles without any failures compared to 75K cycles unlubricated. After further internal testing, the customer decided to use NyoGel® 760G for their tin-plated connectors. NyoGel® 760G is now being used in their data center equipment across the world and has successfully restored equipment power reliability to servers that experienced power failures.
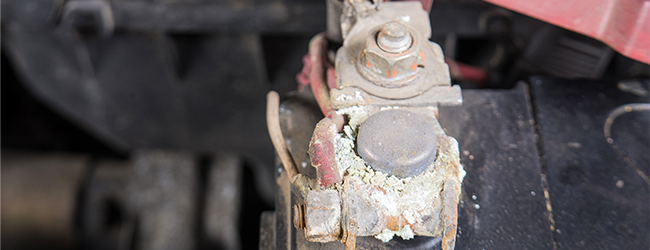
Protecting Battery Terminals Against Corrosion
Background
Commercial vehicles are operated for extensive periods of time under a variety of environmental conditions and depend on reliable components that require shortened and/or infrequent servicing. These vehicles are continuously exposed to road spray, which in the winter contains corrosive salts and chemicals. If a battery or starter terminal were to become corroded, it could cause unwanted downtime as the driver would be unable to start the vehicle or the electronics controls would fail to operate properly. A Commercial Vehicle OEM specializing in Class 6, 7, and 8 trucks approached Nye in search of a lubricant with the right water spray resistance properties to extend the life of their battery, starter & alternator terminals, and ground straps to protect them from corrosion.
Challenge
- Can we provide a lubricant that exhibits excellent water spray resistance while also protecting the terminals from road salt, humidity, and water?
- Can we provide a lubricant that stays in place and exhibits limited oil separation?
Solution
NyoGel® 760G
A silica thickened, medium viscosity, synthetic hydrocarbon grease.
- Excellent water spray resistance
- Superior corrosion protection
- Low oil separation
- Provides lifetime lubrication for lasting connections
- OEM Specifications: Ford: WSB-M1C239-A, GM: 9986087, & FCA: MS-9496
Results
Nye completed 30-day salt spray and cyclic corrosion testing on both nickel brass and tin copper terminals. After testing several greases in our line of connector lubricants, the customer decided to go with NyoGel® 760G as it passed their corrosion and water spray requirements at an appropriate price point.