Advanced Validation Testing for Emerging Technologies
Engineers designing e-mobility solutions and next generation technologies are all tasked with doing more with less. Advanced lubricants are often required to reduce temperatures, weight, torque or other factors that could interfere with achieving high-performance standards. Additionally, as these designs become increasingly electrified, protecting connectors against electrical failure is also a growing concern. Existing solutions need to be validated to new operating extremes or new products may need to be developed to accommodate these demanding operating requirements.
Developing new technologies often means going where no one has gone before. Nye’s engineers work in tandem with our chemists to provide application-specific information that informs the development and validation of our products. With Nye’s modular test apparatuses, environmental chambers, and even custom test apparatuses, we can simulate our customers applications and ensure our lubricants meet their performance standards. At Nye, we can test from a conceptual level all the way up to the actual customer’s components. Some of our advanced test apparatuses include:
Terminal Fretting Test Apparatus for Connectors
Electric Motor Efficiency Apparatus
Electric Power Steering Test Suite
As Electric Power Steering systems become more common and advanced, test data plays an important role in ensuring the lubricant selected for these systems will protect components, reduce risk, and improve safety.
The capabilities within this testing suite allow Nye’s Application engineers to test various designs and geometries of customer EPS systems in a variety of loading and environmental scenarios. Data generation consists of, but is not limited to: efficiency, torque stability, gear mesh interface temperature, and wear analysis. Our EPS Test Suite is composed of three separate apparatuses that accurately simulate EPS operations: a Magnetic Brake System, On-Road Conditions, and a Parking Check.
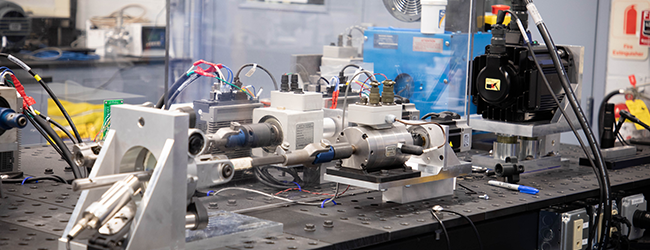
Magnetic Brake System
Our magnetic brake system simulates an OEMs ‘run-in’ process. This is a high load, high speed, test entirely dedicated to removing high spots—or residual imperfections from the manufacturing process. When high spots are removed, it allows our engineers to understand how our lubricants will perform in an aged EPS system.
On-Road Conditions
This apparatus simulates routine operations. It uses a feedback loop with two server motors that rotate from 0-540 degrees at 30 rotations per minute. Engineers can then use the feedback loop to simulate specific loads at different wheel rotations. OEMs are constantly trying to create systems that operate at higher loads. Our apparatus can simulate loads of up to 120 newton-meters to simulate the different EPS load requirements. Using the infrared camera, our engineers can see the temperature distribution of the entire gear assembly. This allows us to assess how well our lubricants are reducing the amount of heat generated by the motor under specific loads and wheel rotations.
Parking Check
This apparatus is a non-loaded Parking Check, also known as a Backdrive Check. This uses a high-resolution torque transducer to assess gear-to-torque distribution when a wheel is turned all the way in one direction. With this information, our engineers can remove the peaks and valleys of that distribution data to obtain the average gear-to-torque distribution for the system. This test allows us to understand frictional characteristics in EPS systems and how they affect the “feel” of steering.
Terminal Fretting Test Apparatus
Fretting wear is one of the major forms of electrical deterioration and failure in a variety of industries, including Automotive, Aerospace, and Consumer Electronics. Fretting wear refers to a mechanical and chemical wear mechanism where the sliding contact between two surfaces creates wear, which becomes oxidized. This process continues at an exponentially higher rate once oxidized wear particles are created. The failure mechanism occurs when enough oxidized wear debris has been created and the contact resistance increases to a level where continuity in the contact is lost. The good news? Fretting wear is preventable with the right lubricant!
With Nye’s fretting test methodology and apparatus, we can determine the durability and reliability of our lubricants in a real-world fretting environment. Through the testing of lubricants to their ultimate fretting failure point, we can look forward to helping our customers design systems that are optimized with a lubricant to reduce or eliminate fretting failures. This can lead to a reduction in the warrantee and safety issues.
Our modular fretting test apparatus, or multi-terminal fretter, allows us to test a variety of components and geometries to ensure our lubricant will outlast your component life requirements. Standard geometries include: cylinder on cylinder, ball on disc, and electrical terminals, but we can accept a wide variety of geometries and supplied components.
Electric Motor Efficiency Apparatus
The ADVT Lab has developed an Electric Motor Efficiency apparatus aimed at optimizing the efficiency of Nye products intended for small electrical motors, actuators, and servos. Reducing power consumption while providing extended life performance in these applications is critical in the success of Electric Vehicle platforms.
ROF+ Bearing Test Apparatus
As bearings are pushed to higher speeds at higher temperatures, lubricant degradation is a concern to many bearing manufacturers. A way to measure bearing life, therefore, is critical. The R0F+ Bearing test apparatus tests the functionality and life of lubricating greases in rolling bearing applications at various conditions. The ROF+ tests lubricating greases at speeds up to 25,000 RPM, temperatures up to 230 °C, radial loads of 50 to 900 N, and axial loads of 100 to 1,100 N.
The standard bearings are 6204 deep groove ball bearings or 7204 angular contact ball bear rings, but other geometries including customer supplied bearings can be utilized. Using this test, we estimate the grease life, temperature limits, and speed factor (NDm) for our products that are to be used in bearing applications.
Custom Solutions
Nye’s Application Engineers will work with you to design and build custom test equipment that validates our lubricant for your application. With our custom modifications and a collaborative partnership, we can ensure that the test apparatus meets your application requirements. Nye engineers are currently using the data collected by our test apparatuses to formulate next-generation greases for our customers designing emerging technologies.
Want to learn more or discuss testing solutions? Contact Us.